Blog
Mit Vollgas zu individuellen Bauteilen
Thomas Niklaus vom Unternehmen NiRep ist nicht nur Landmaschinen-Profi, sondern auch leidenschaftlicher Tractor-Pulling-Fahrer. Ob Reparaturservice für seine Kunden oder hochbelastbare...
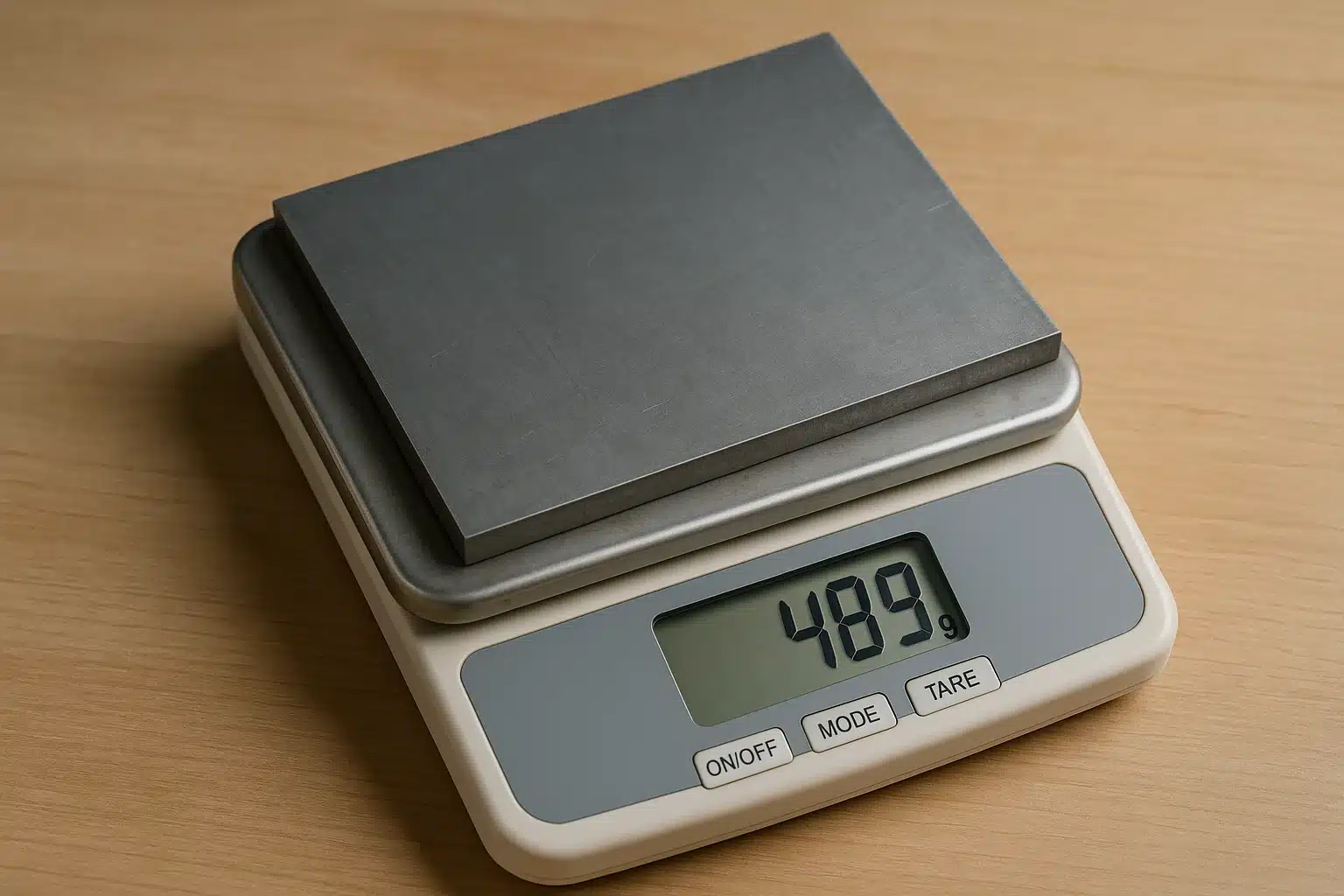
Bauteil Gewichtsrechner
Ein Gewichtsrechner für Metallteile bzw. Blechteile ist ein praktisches Online-Tool, mit dem sich das Gewicht von Blechen, Rohren oder anderen Metallbauteilen schnell und zuverlässig bestimmen...
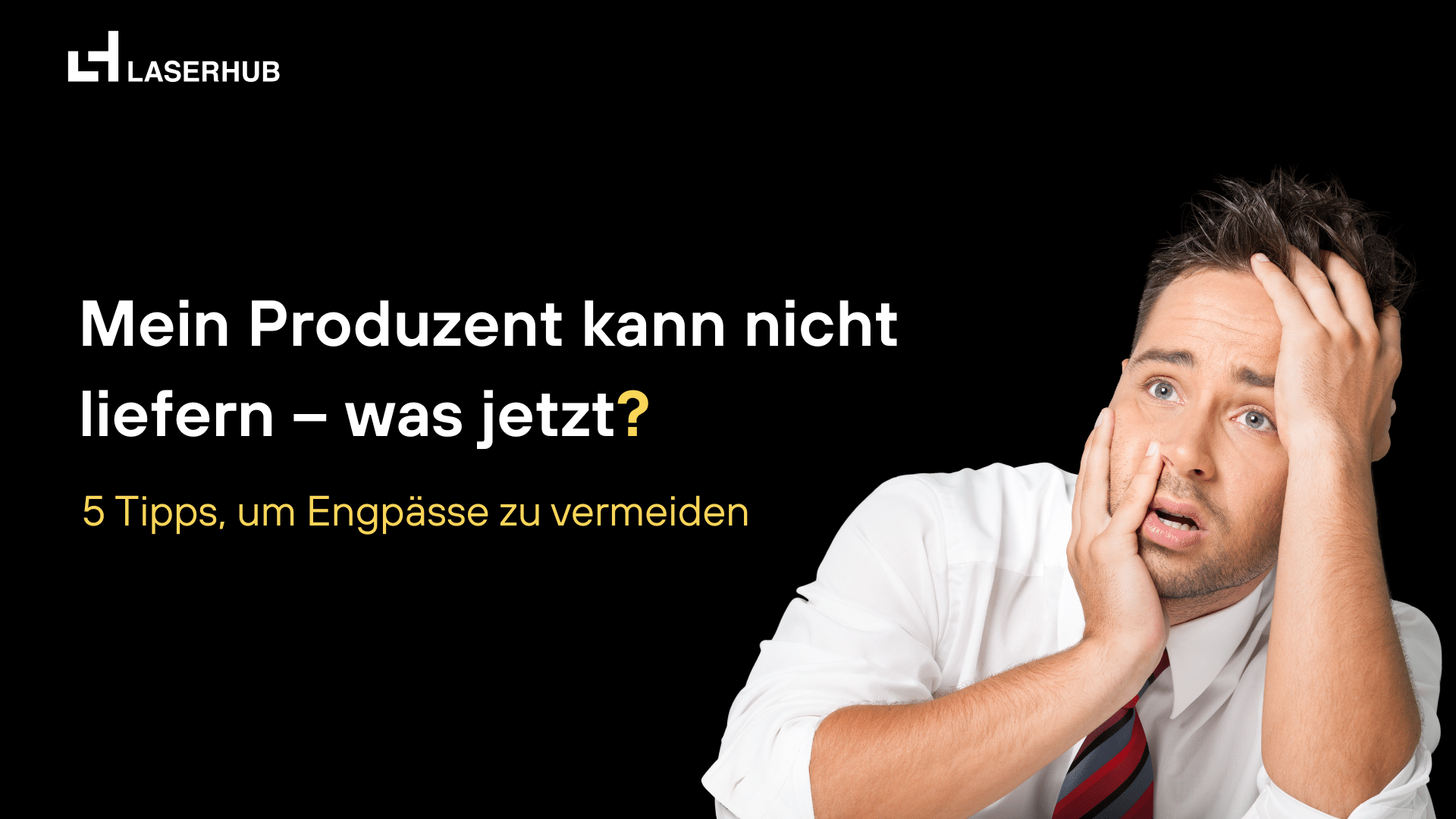
„Unser Produzent hat dicht gemacht“ – Was Unternehmen jetzt brauchen, wenn eingespielte Prozesse plötzlich wegfallen
Es ist eine Situation, die wir bei Laserhub aktuell immer häufiger hören:
„Wir haben seit Jahren mit einem kleinen Metallzulieferer hier aus der Region gearbeitet. Die Zusammenarbeit war...
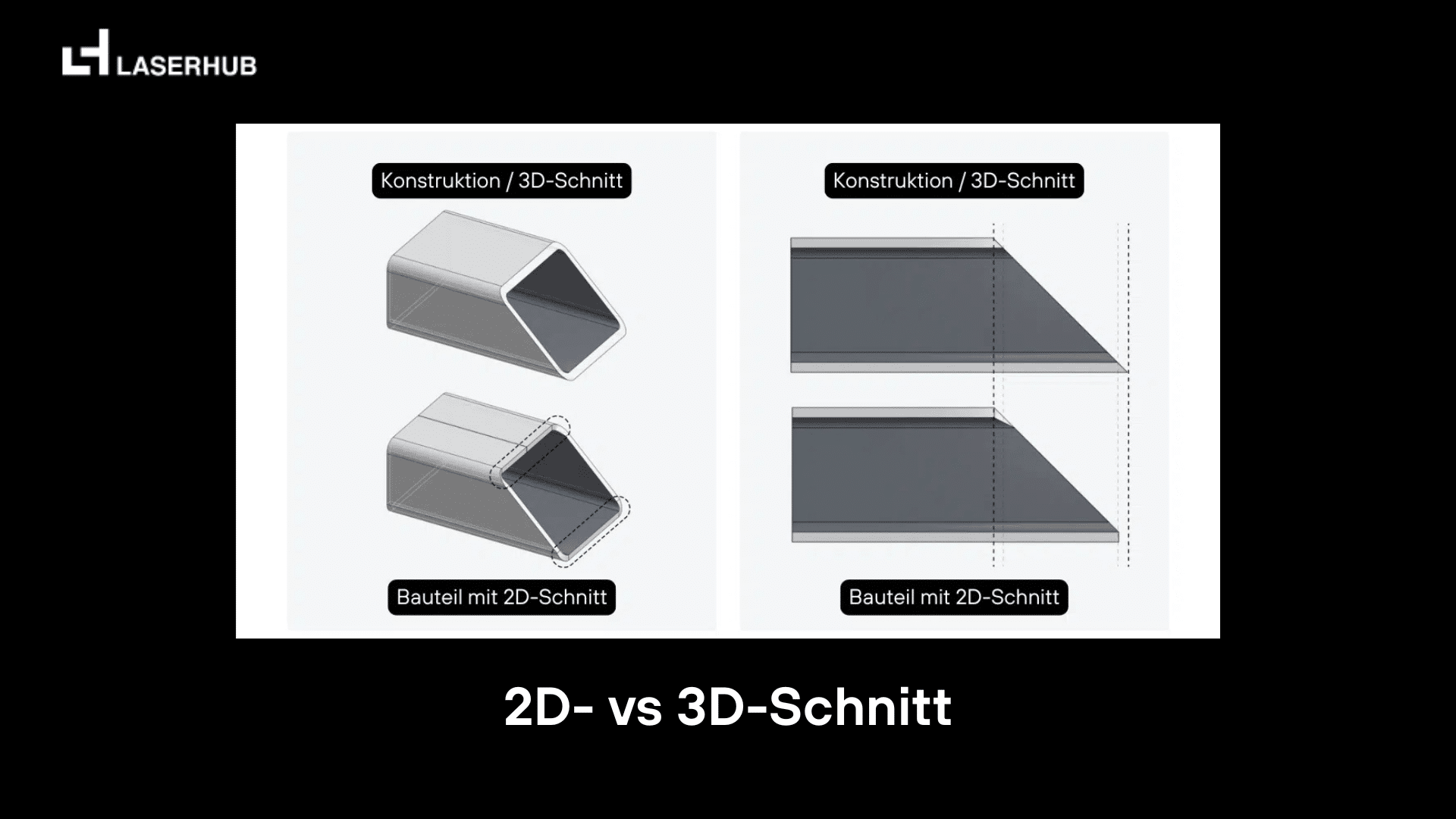
Rohrlaserschneiden: Wann 2D- und wann 3D-Schnitt nutzen?
Das Rohrlaserschneiden hat sich als eine der effizientesten und präzisesten Methoden zur Bearbeitung von Metallrohren etabliert. Ob für den Maschinen- und Anlagenbau, den Metallbau oder die...
Wenn sich das Bestellvolumen plötzlich mehr als verzehnfacht
Manchmal kommt der Erfolg gefühlt über Nacht: Wie bei PUSH components, einem Unternehmen, das gut durchdachte Produkte für Campingbusse herstellt. Nachdem Influencer den einzigartigen...
Neue US-Zölle auf Stahl und Aluminium: Was bedeutet das für Europa?
Die globale Metallindustrie steht erneut vor Turbulenzen, da die USA neue Zölle auf Stahl- und Aluminiumimporte verhängt haben. Mit einem Zoll von 25 % auf Stahl und 10 % auf Aluminium stehen...
Von der Kinderkrankenschwester zur Metallexpertin
Der Fachkräftemangel trifft die Metallbranche zunehmend. Deshalb müssen Unternehmen neue, innovative Wege gehen, wie zum Beispiel XPROMA. Der Anbieter von Verpackungs- und Sortiermaschinen sowie...
Jetzt Stahlpreise für 2025 sichern?
Die Stahlpreise haben in den vergangenen zehn Jahren starke Schwankungen durchlaufen und weltweit Unternehmen beeinflusst. Wir haben uns mit Christian Gebhardt, Metalltechnologie-Experte bei...